This has been the battle cry heard throughout the industry for years, demanding the next evolution in additive manufacturing; the ability to 3D print your parts, fixtures, tooling, whatever you want, in real metal. DMLS (Direct Metal Laser Sintering) systems have blazed the way with gigantic machines using highly hazardous materials, insane lasers, and a price tag upwards of $1 million. These machines are amazing, there is absolutely no question about that. And, in the immortal words of Ferris Bueller, “If you have the means, I highly recommend picking one up.”
But what about the rest of us? What if we don’t want to don a hazmat suit just to print our part? What if we don’t have seven figures to spend on a metal printer? Markforged has heard you, and has brought metal 3D printing to the masses with their end-to-end metal 3D printing solution, the Metal X.
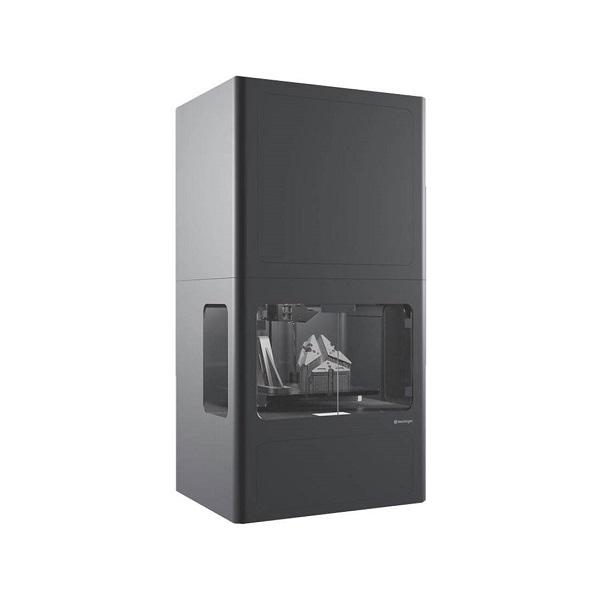
What’s the Advantage?
The advantages of 3D printing in metal are many of the same that exist for 3D printing in plastic or composite: geometries impossible with subtractive manufacturing, quick design-to-part, exponentially more cost effective than traditional machining, the list goes on. And now, you have all of those amazing advantages while getting a real, honest-to-goodness, metal part that can take the punishment, heat, stress, and pressure that even the impressively strong Markforged Composite parts just can’t handle.
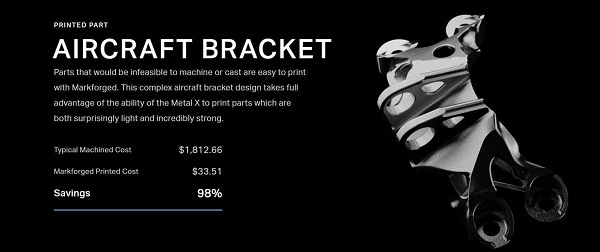
What sets the Metal X apart from the metal 3D printing competition is its ability to print in high resolution without using hazardous loose powdered metals or high wattage lasers. It is also a complete system from design to part. Shockingly, some competitors only offer half of the process, leaving the customers to fend for themselves in terms of completing the part. The Metal X also prints lighter and more cost effective parts than many competitors by allowing closed-cell infill structures (which even DMLS systems can’t offer,) and there are no hazmat suits required.
Oh, and did I mention the Metal X is roughly 90% cheaper than your average DMLS system?
What’s Under the Hood?
The Metal X is one part of a three machine solution that includes the Metal X printer, the Wash-1 Wash Station, and the Sinter-1 or the larger Sinter-2 sintering unit specifically designed and engineered for the Metal X printer. This system includes all of the machines needed to go from design to part quickly and easily while proving to be one of the most reliable, easy to use and cost-effective ways of printing metal parts.
At the heart of the Metal X system is the FFF extrusion technology, that Markforged has perfected with their award-winning composite printers, dialed up to 11. The build chamber is precisely temperature controlled and the build tray is held to the bed using a vacuum system. The Metal X builds its parts layer by layer at a resolution of up to 50 micron, (.002”) extruding a filament of metal powder bound in plastic. The part files are automatically and precisely scaled up in the highly-intuitive Eiger printing software to account for shrinkage during the sintering process that will take place after the printing.
Once the printing process itself is completed, you are left with what is known as a “Green Part.” The part is fragile at this stage and is composed of the metal powder still suspended in the plastic matrix. The part is also slightly larger than your part’s desired size due to the presence of that plastic matrix. The green part is placed in a wash station that removes much of the plastic matrix that is binding the metal powder together and once finished in that bath the part is placed in a specially designed sintering oven that is automatically calibrated specifically for the part or parts being sintered. The sintering oven heats the parts to more than 1300 degrees Celsius, removing the remaining plastic binder and melting the powdered metal, fusing it into a precise, solid metal part.
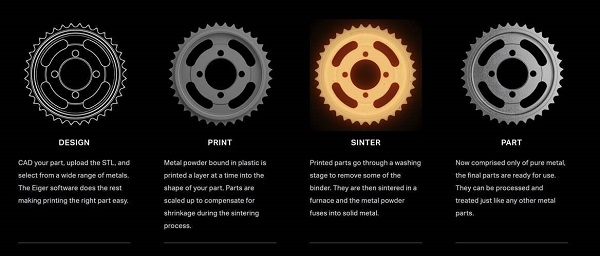
Once cooled, your part is done and ready for use. The high resolution of the Metal-X leaves you with a part nearly devoid of layer lines creating a surprisingly smooth attractive part with little to no post-processing required, however, if desired, parts can be postprocessed just like metal, because they are metal. Speaking of which, currently the Metal X prints in 17-4 Stainless Steel offering high strength, high hardness, and excellent corrosion resistance. Newly released is the ability to print in H13 tool steel. Optimized for high temperature and wear applications, H13 is used for molds and die casts, wear inserts, tooling, and forming punches and dies.
In Beta, and coming soon, are the following:
- 316L Stainless Steel
- A2 Tool Steel
- D2 Tool Steel
- Ti 6-4 Titanium
- Inconel 625
- Copper
I Want One!
Of course you do. To get more details, learn even more about the technology, or get a quote, I encourage you to reach out to our 3D printing team at GSC. Our own Metal X machine will be arriving at our Germantown Technology Center soon, so stay tuned!
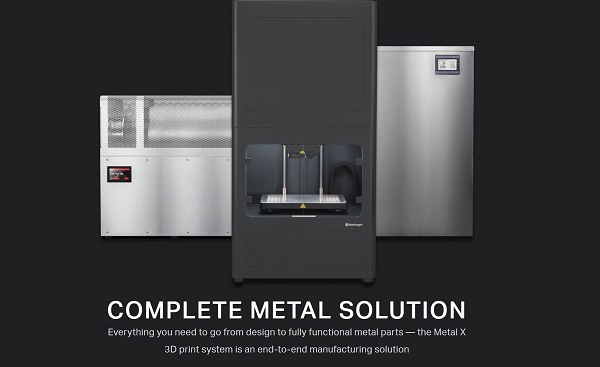
Share
Meet the Author