The manufacturing industry continues to evolve at a rapid pace, and as we head into 2025, several engineering trends are poised to redefine how products are designed, manufactured, and delivered. These innovations not only address current challenges but also pave the way for more sustainable, efficient, and resilient production systems.
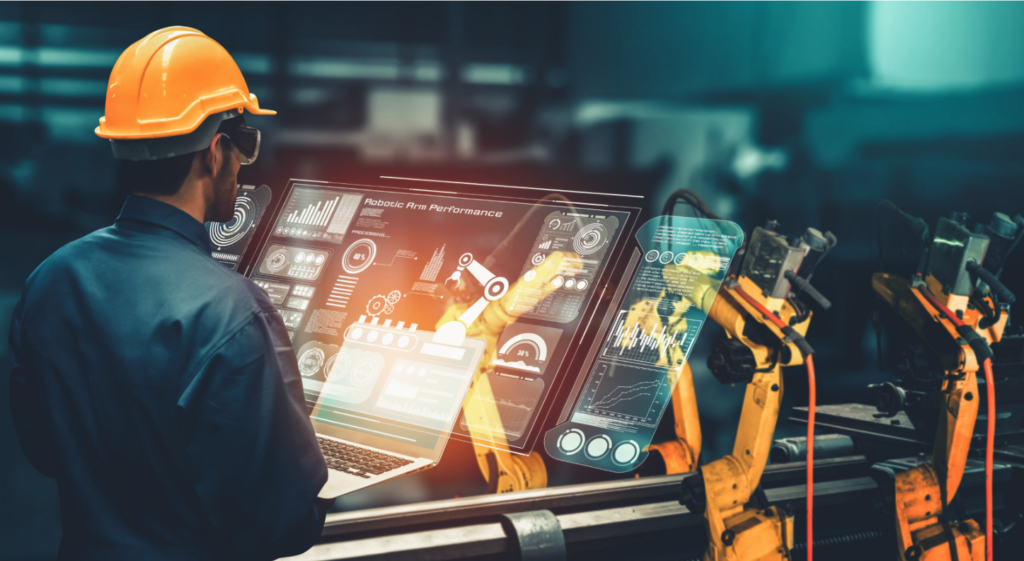
Here’s a look at the top engineering trends shaping the future of U.S. manufacturing in 2025…
1. AI-Driven Manufacturing Processes
Artificial intelligence (AI) is no longer a futuristic concept—it’s a reality that’s transforming manufacturing. In 2025, we expect to see AI being increasingly integrated into manufacturing operations for predictive maintenance, quality assurance, and production optimization. AI-powered systems can analyze vast amounts of data in real-time, reducing downtime and improving product consistency.
Example Applications:
- Predictive analytics to anticipate equipment failures.
- AI-driven quality control using computer vision.
- Adaptive production lines that respond dynamically to demand changes.
2. Advanced Robotics and Automation
Robotics and automation continue to evolve, offering unprecedented precision and efficiency. Collaborative robots (cobots) are becoming more sophisticated, working alongside human operators to enhance productivity and safety. By 2025, the integration of robotics in smaller-scale manufacturing will become more accessible due to decreasing costs and increased usability.
Trends to Watch:
- Greater adoption of cobots in SMEs (Small and Medium Enterprises).
- Enhanced robotic dexterity for complex tasks.
- Robotics-as-a-Service (RaaS) models enabling flexible deployments.
3. Additive Manufacturing Matures
Additive manufacturing (3D printing) is no longer just for prototyping. In 2025, it’s becoming a mainstream production tool, especially for custom parts, low-volume production, and complex geometries that traditional manufacturing struggles to produce. Advances in materials science are also expanding the range of printable materials, including metals, ceramics, and composites.
Key Developments:
- Multi-material and large-format 3D printers.
- Use of 3D printing for end-use parts and tooling.
- Integration with traditional manufacturing processes.
4. Sustainability and Circular Manufacturing
Sustainability is a top priority for manufacturers in 2025. From reducing waste to minimizing energy consumption, engineering solutions are focusing on building a circular economy. This includes remanufacturing, recycling, and designing products with end-of-life in mind.
Sustainable Practices:
- Adoption of energy-efficient production technologies.
- Increased use of recycled materials in production.
- Life-cycle assessment tools for better environmental decision-making.
5. Digital Twins for Real-Time Optimization
Digital twins—virtual replicas of physical systems—are revolutionizing how manufacturers monitor, simulate, and optimize operations. By 2025, digital twins will be more widely adopted, allowing for real-time insights and predictive modeling to enhance efficiency and reduce costs.
Applications:
- Simulating production scenarios to optimize layouts.
- Monitoring equipment health in real time.
- Accelerating product development cycles.
6. Cybersecurity for Smart Manufacturing
As manufacturers embrace Industry 4.0 technologies, cybersecurity becomes a critical focus. The interconnected nature of smart factories increases vulnerability to cyber threats. In 2025, manufacturers are expected to invest heavily in securing their systems through advanced encryption, secure data protocols, and employee training.
Cybersecurity Strategies:
- Implementing AI-driven threat detection systems.
- Regular audits of IoT devices and networks.
- Enhancing employee awareness of cyber hygiene.
7. Workforce Transformation and Skills Development
The manufacturing workforce is undergoing a significant transformation. With the adoption of new technologies, the demand for skilled labor is shifting toward roles that require expertise in digital tools, robotics, and data analytics. Upskilling and reskilling initiatives will be critical for addressing these changes.
Focus Areas:
- Partnerships between industry and educational institutions.
- On-the-job training programs for emerging technologies.
- Emphasis on STEM education and diversity in manufacturing roles.
Conclusion
The trends shaping U.S. manufacturing in 2025 highlight an industry that is becoming smarter, greener, and more adaptive. By leveraging advancements in AI, robotics, and additive manufacturing, while committing to sustainability and workforce development, manufacturers can position themselves for long-term success. The future is bright, and 2025 promises to be a pivotal year for engineering innovation in manufacturing.
Share
Meet the Author