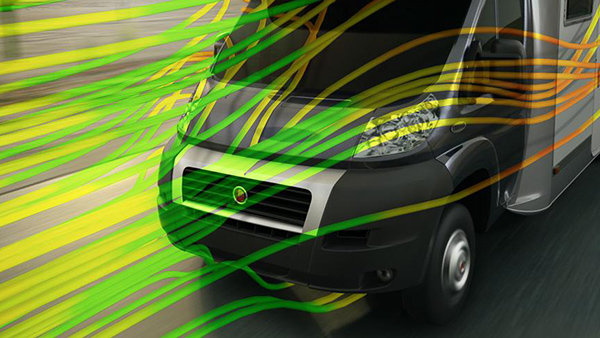
While we are in an era of high inflation, we still have tools that can lower our material costs. Depending on your industry, Computational Fluid Dynamics may be a concept that has been used for decades, or it might be a brand-new term. In this blog, you will gain an understanding of the software, its functionality, and its potential applications for thermal management, pump or fan cost reduction, cooling efficiency, and more.
Computational Fluid Dynamics Brief Background
60 years ago, people such as Francis H. Harlow, A.M.O. Smith, and John Hess were working to develop numerical methods for computers that could solve problems in aerodynamics. Their early efforts were for the aerospace industry but laid the foundations of Computational Fluid Dynamics, often called “CFD,” for short. Any accuracy shortcomings came from a struggle with computing power in their day, which we no longer confront today.
In the last 60 years, Computational Fluid Dynamics has moved on from aerospace and automotive aerodynamic challenges to a wider range of problems, including but not limited to:
- Electronics Cooling
- Predicting pump and pressure requirements
- Optimizing dispenser nozzles
- Sizing fans
- Looking at gas flows
- Optimizing cooling for molds
- And even understanding how to move non-traditional fluids like melted cheese or chocolate
When referring to Computational Fluid Dynamics, we are talking about a methodology for solving these problems. There are different software tools, including SOLIDWORKS Flow Simulation, a modern CFD tool integrated into SOLIDWORKS, making it seamless within the CAD environment.
See what SOLIDWORKS Flow Simulation can do, in this video:
SOLIDWORKS Flow Simulation = Lower Product Costs
Customers repeatedly tell us that keeping their product costs down is becoming a challenge. With the need to keep costs low during a period of inflation, the demand for this tool has greatly increased. Fortunately, simulation software, such as SOLIDWORKS Flow Simulation, has been solving these issues for many years.
Here are a few ways SOLIDWORKS Flow Simulation can help you save money on your designs:
- Optimizing fan sizes
- Decreasing electronic housing sizes while still ensuring proper cooling
- Optimizing pump sizes
- Creating new designs that lower the energy requirements
- Creating faster cycle times by optimizing cooling in manufacturing processes
As you can see, SOLIDWORKS Flow Simulation has applications for anyone with electrical components in their design, particularly when it comes to thermal management. One of the main features to note is the accuracy of the software. With the precision of these tools, you can have access to the information you need earlier in the design process.
Know exactly how your design will perform before creating a prototype with the ability to make design changes while simulating. With SOLIDWORKS Flow Simulation, you can make smarter decisions, avoid design rework, and produce the best version of your product on the market.
Predict Product Performance with SOLIDWORKS Flow Simulation
GSC has worked with customers who predicted operating temperatures accurately within a few degrees (Fahrenheit) of actual operation. With such accuracy, they could drastically reduce the number of prototypes and lower costs. While the accuracy of designs can be affected by the environment they are placed in; we can help you evaluate those factors during the investigation of the tool.
In the image below, the accuracy of SOLIDWORKS Flow Simulation is displayed against experimental results. The red dots represent predicted values, and the black lines show the calculated values. Differences can be explained by manufacturing variations from models, imperfect boundary condition definitions, and material/environmental variation. Increases in accuracy are possible but require more time for modeling and considering boundary conditions.
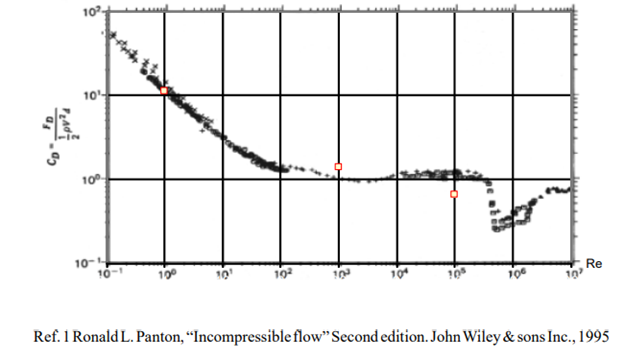
Best-in-class companies are near-universal in their usage of simulation software and that is because of its high level of accuracy. The accuracy of the tool in SOLIDWORKS Flow Simulation is like knowing the future providing you with the information you need to make the right decisions. Learn more about the benefits, here.
Contact Us
Increase your productivity and reduce costs with this easy-to-use tool. Have a question? Contact the Simulation Team with questions or set up a Hands-on Test Drive to try the tool yourself.
Want More?
If you’re interested in learning more, check out these additional resources below:
Share
Meet the Author