
From Prototyping to Printing Truly Functional Production Parts
GSC customer Johnson Level, a leading provider of levels, lasers, and layout tools, has been using their Markforged Mark Two industrial-grade 3D printer for many projects. Within the first 9 months, they implemented new composite material parts on at least 4 production projects and saw a 90% cost reduction where expensive tooling could be replaced.
Whether for ultrasonic welding and fixturing, end of arm tooling, or in packaging and assembly, they continue to find applications for high-strength composite printing.
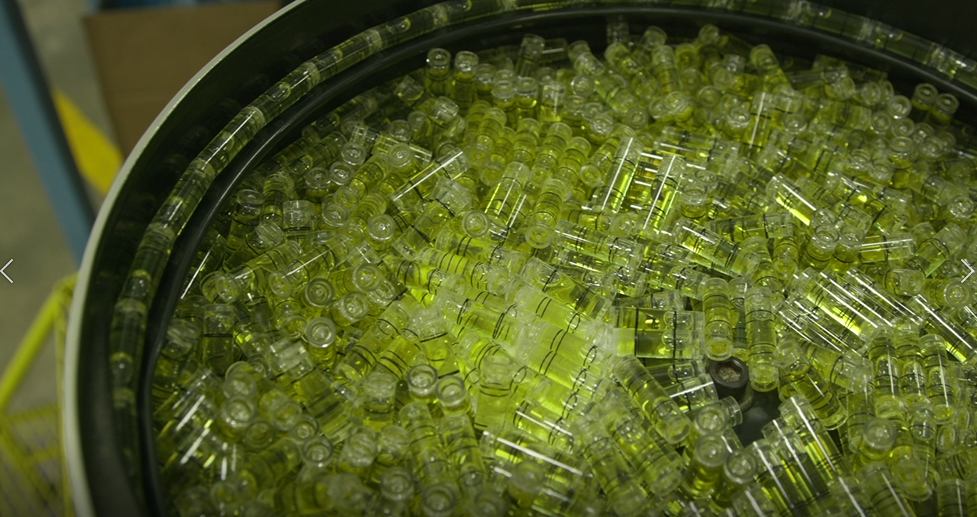
According to Johnson Level’s Director of Operations Adam Ruback, the benefits of shifting to this method of 3D printing made the most sense:
“I attended an event and saw 3D carbon fiber printing technology used, and used in other industries to create fixtures and prototypes and thought it would be a really useful machine here at our facility in Mequon. I saw the opportunity that we could bring something in-house here to really push us to the next level.”
If you’re curious what composite materials are, or what carbon fiber reinforcement is, check out this handy blog “Stronger, Cheaper, Better: Markforged 3D Printed Parts” by our Application Engineer Nick Schmidtke. He details the strength and overall benefits of these materials.
“Because of 3D printing we’ve reduced our costs by nearly 90 percent. 3D printing is part of a design process. If you’re not 3D printing, you’re going to be left behind”
– Tim Wojo, Johnson Level’s
Quality Design Engineer
Watch to Learn from Johnson Level Employees
Johnson Level used Onyx filament (nylon and chopped carbon fiber) and a few of these parts had continuous carbon fiber reinforcement. The ultrasonic welding fixture, in particular, did.
Applications for Composite Parts
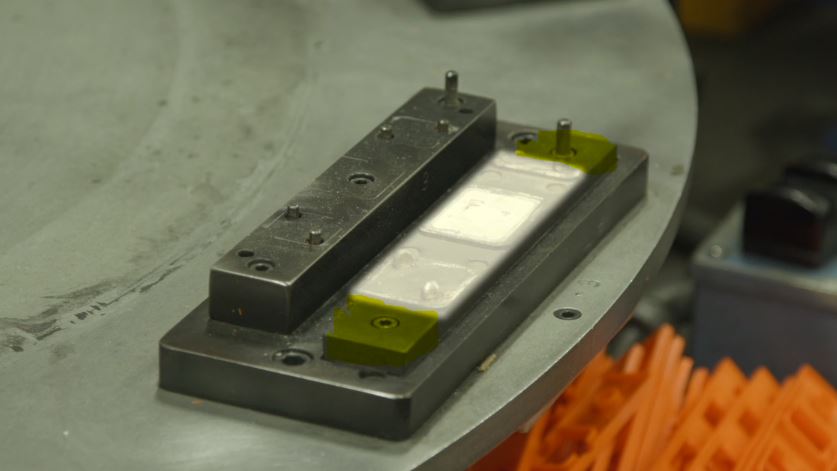
At one station, there’s a vibration at a high frequency to weld components together. To prove the value of the Markforged material and printer before their purchase, Johnson Level was able to print a sample part with our help on GSC’s machines and try it at their Mequon location. It proved to be as durable as their current fixtures and a cost-saving option.
Other advantages Johnson Level found were the ability to print parts overnight, saving lead time and cost. Design changes were convenient and quick to make, whereas before the process was anything but quick.
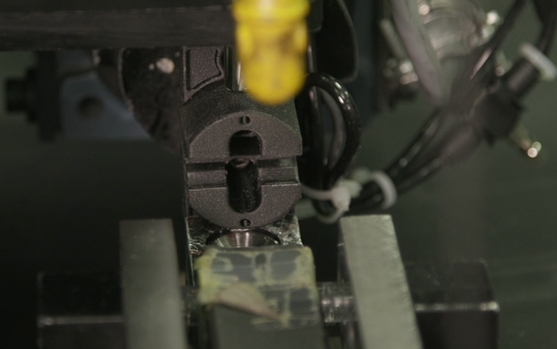
They reduced lead times from weeks to days, and in many instances, hours. For example, in their vial filling station, they have grippers that mechanically move parts into position. The grippers are a wear item and the previous method of machining them out of steel was fairly expensive for replacements and had a long lead time.
By switching these grippers to being 3D printed with Markforged material, they saved on weight and improved the lifetime of the part.
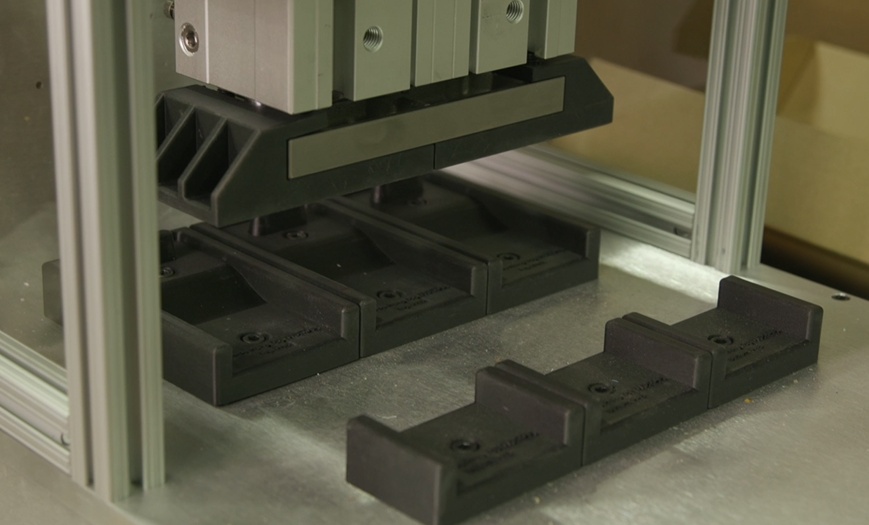
With Markforged, Johnson Level printed components they couldn’t machine. They printed nests in different applications, including in a machine prototype built to assist with packaging and assembly. The machine was built in a week, instead of up to 12 weeks.
Part storage, or lack-there-of, was another benefit. Spare parts can be stored in a computer instead of on the shelf.
Next Steps with 3D Printing
“We’ve adopted this technology less than a year ago. We’ve already proved it out in numerous projects. It’s paid for itself already, and we’re only beginning to scratch the surface of what this technology can actually do for us”
– Adam Ruback
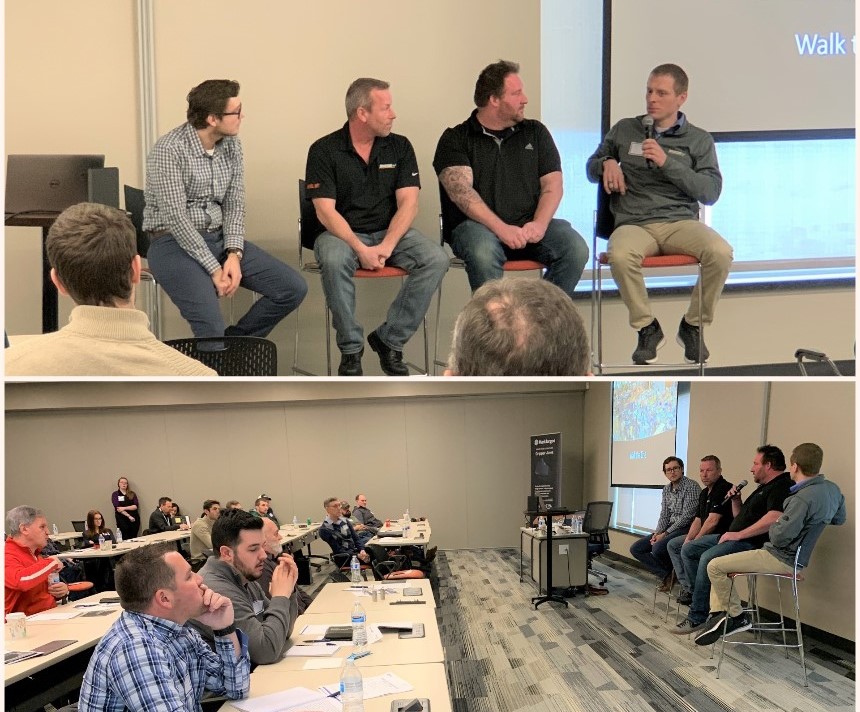
Johnson Level has looked at adding a new 3D printer to give them more capacity to print some of their bigger products. They are continuously experimenting and finding ways to use the printer to improve workflows, ergonomics and workplace conditions, costs, and lead times.
About 3D Printing with GSC
There are a variety of ways you can take advantage of 3D printing.
“We’ve used GSC to run FEA analyses for us, and they act as almost an extension of our team. They know our product line well, and for us, it’s a huge benefit to have somebody that knows that and can step in and help you out” – Dave Mencel, Johnson Level’s
Product Development and R&D Manager
We understand times are ever-changing, but if you’re looking for an affordable entry into 3D printing, Markforged is a viable option for you and your company. Markforged entered the 3D printing space and became a differentiator precisely because they make affordable 3D printers compared to their competitors.
Markforged offers unique patented technology with reinforcement fibers that make their parts very, very strong. Often, as strong as metal (and lighter)! Having such a wide selection of materials is amazing, as well.
Please let us know if you would like to:
- Learn more about Markforged and get educational info emailed to your inbox
- Talk over the phone with our Application Engineer to identify possible applications in your line
- Get a sample part of yours printed to prove material strength and ROI
- Virtually attend a free, short-and-sweet webinar with our 3D printing team
Anything you need, we’re here to help!
About Johnson Level
We’re especially grateful to Johnson Level for sharing this story. We appreciate their willingness to experiment, share their applications, and embrace 3D printing as a part of their process improvement. They successfully targeted areas of their production line to optimize composite part replacements and saw amazing results.
- Learn more about Johnson Level: www.johnsonlevel.com
- Learn more about Markforged: www.gsc-3d.com/additive-manufacturing/markforged
- Learn more about us, GSC: www.gsc-3d.com/about
Contact Us
Have a question? We’re always available to talk over the phone, for you to leave a message, or for you to submit a request – just contact us.
Share
Meet the Author